Comparison of Single Stage and Two Stage PET Bottle Blow Molding Processes
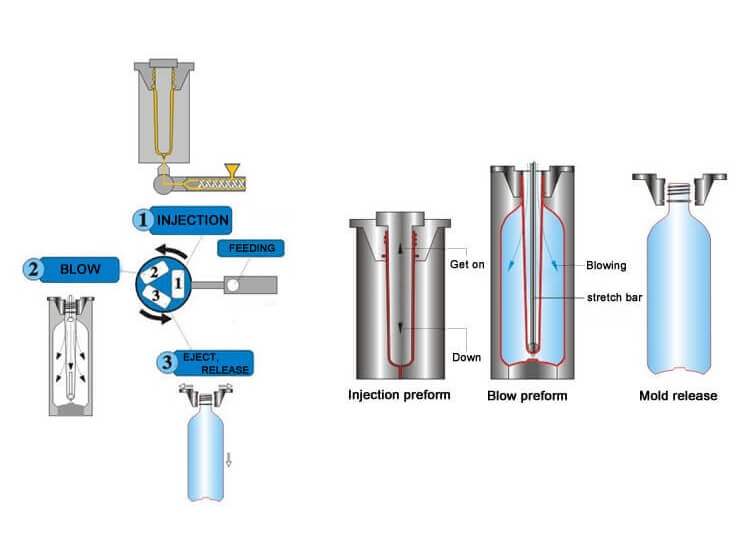
Stretch blow molding plays a pivotal role in crafting PET (polyethylene terephthalate) bottles, extensively utilized in packaging water, juices, and various plastic products. Since its inception in the early 1970s, this method has gained significant traction, notably in producing carbonated beverage bottles like Coca Cola. One of its prime advantages lies in its ability to stretch the preform both axially and in the hoop direction. This stretching enhances the container's tensile strength, barrier properties, drop impact resistance, and top load strength. Consequently, it often leads to a 10 to 15% reduction in the overall weight of the container, making it an environmentally friendly choice.
Stretch blow molding is broadly categorized into two types: Single-Stage Blow Molding and Two-Stage Blow Molding.
Single-Stage Blow Molding
In this approach, an extruder injects plastic into a preform mold, rapidly cooling it to create the preform. Subsequently, the preform is re-heated and placed in the container mold. Hot air is then introduced into the parison, causing it to stretch into the shape of the bottle. Once cooled, the mold is opened, and the finalized bottle is extracted. This method suits various applications, particularly for wide-mouthed jars and scenarios where exceptionally high production rates are not necessary.
Two-Stage Blow Molding
The two-stage process involves two machines: an injection molding system and a stretch blow molding machine. In the first machine, plastic is injected into a fully cooled preform, which is then transferred to the second device. The preform typically includes the bottle's neck and threads and can even be sold to a third-party vendor before being blown using the second machine. Upon arrival at the second machine, the preform is unscrambled, reheated with infrared light, conditioned, and then molded. The name "cold preform method" is derived from the need to cool the preform before reheating and stretching.
Process Involved in Two-Stage Method:
- Dehumidification and drying of PET material.
- Injection of superheated raw materials into the preform mold.
- Cooling of melted PET to room temperature.
- Processing the preform using a finishing machine.
- Reheating the preform in the stretch blow molding equipment.
- Using metal blow molds to blow compressed air into the bottles.
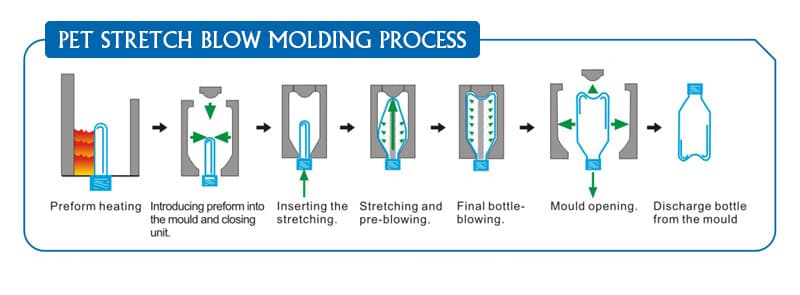
Advantages of Two-Stage Molding over One-Stage:
The choice between single-stage and two-stage molding processes depends on the product/application. Approximately 80% of the 580 billion plastic bottles consumed globally in 2021 were for beverages and commonly manufactured using the two-stage technology due to factors like tool prices, capital expenditure, and available preforms. Two-stage molding is often favored due to its cost-effectiveness, particularly for high volumes. On the other hand, the single-stage process is suitable for crafting custom bottle designs in limited numbers where specific bottle features are a priority.
In conclusion, the selection between single-stage and two-stage stretch blow molding depends on the desired bottle features, production volume, and economic considerations. Each method offers distinct advantages, and understanding these factors is crucial for making an informed decision in PET bottle manufacturing.
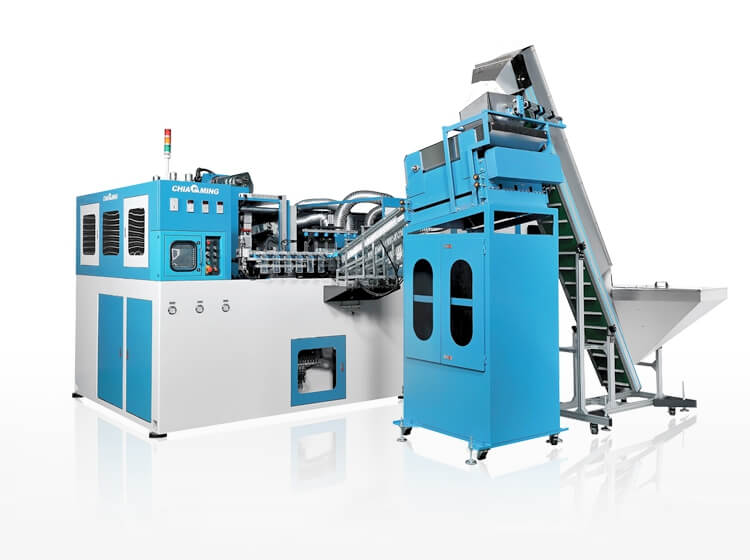
Comparison Table: Single-Stage vs. Two-Stage Blow Molding
Feature | Single-Stage Blow Molding | Two-Stage Blow Molding |
Process |
|
|
---|---|---|
Applications | Suitable for various applications, particularly for wide-mouthed jars, and scenarios where exceptionally high production rates are not necessary. | Typically suitable for high-volume production, often preferred due to cost-effectiveness factors such as tool prices, capital expenditure, and available preforms. |
Cost-effectiveness | Relatively higher production costs, are suitable for small-batch production of custom bottle designs where specific bottle features are a priority. | Relatively lower production costs, particularly suitable for high-volume production. |